There are two types of senior executives: those who value their workers’ opinions and ideas on how to improve business — and those who don’t, primarily because they’re convinced they have all the answers. Cargill Value Added Meats’ (CVAM) complex in Waco, Texas, values its employees and its Valuing Imagination in People (VIP) program has yielded some impressive results.
Under its VIP program, ideas on how to improve working conditions or save money in operations are submitted by facility workers and a committee reviews them. Anyone submitting an idea gets a $10 retailer gift card. From that point, ideas are recognized with a $100, $150 or $500 gift, depending on the value of the idea.
One employee submitted an idea on how to place product on cooking racks to prevent bright spots, or touchers, which are created when two pieces of product touch on the rack. “We eliminated touchers by stacking products in a different pattern on the rack,” says JR Dollins, continuous improvement manager at the complex, who is also a certified Six Sigma Black Belt and a 17-year Cargill veteran.
Other employee ideas have saved the Waco complex anywhere from $800 to $150,000 a year, adds Paul O’Leary, operations manager and 20-year Waco complex veteran.
Throughout the decades, the Waco facility has evolved into a 381,275 sq. ft. poultry and meat complex. The plant offers a range of raw and pre-cooked value-added turkey, beef, pork and chicken products. This complex is one of nine facilities making up the CVAM retail business. CVAM is a business unit of Wichita-based Cargill Meat Solutions.
Employee ideas on how to improve operations can be submitted in many areas. Turkey (raw and pre-cooked whole birds plus a range of further value-added turkey products) is this complex’s No. 1 protein. It harvests about 28,000 birds a day. But Cargill’s Waco complex also processes a range of value-added beef, pork and chicken. The bulk of the beef is in the form of diced product distributed to industrial customers, the bulk of pork is in ham products and chicken is primarily deli products.
Products made per year at the Waco complex (in descending order of total lbs.) include turkey, 52,593,122 lbs. (66.1 percent of the total production mix); pork, 12,221,785 lbs., (15.4 percent); chicken, 10,228,756 lbs. (12.9 percent); and beef, 4,524,318 lbs. (5.7 percent). Retail products total 60,694,860 lbs. (or 76.3 percent of the total product mix) per year while commercial products amount to 18,873,121 lbs. (23.7 percent). Further processing is budgeted at 80 million lbs. per year; whole-bird processing is budgeted at 105 million lbs. per year.
“Good teamwork imagination will create the value for our customers, employees and Cargill,” says Wesley Carter, complex general manager and 15-plus year company veteran, of the VIP program.
Here’s hoping industry plant management throughout the US adopts some type of program or system — if they haven’t already — that taps into employee ideas on how to improve plant operations. Not only can some of their ideas benefit plants, but the employees’ buy-in and sense of worth regarding plant operations will help improve the company’s overall performance.
(For more information on Cargill’s Waco complex, read “Talking turkey and more” in the June issue of MEAT&POULTRY magazine.)
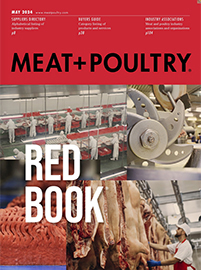