Fifth-generation pig farmers, Tim Beeler and his brothers bought the family farm from their father in the early 1980s. At that time the farm used the conventional method for marketing its products; it loaded meat into a truck and shipped it to a larger packing company. But the conventional approach wasn’t delivering the results the brothers wanted, so they made a decision to go in a different direction.
“We decided to try to market our own product,” says Tim Beeler, president, Beeler’s Pure Pork, Le Mars, Iowa. “At that time the natural and antibiotic-free industries were just starting to evolve, so that’s what we decided was going to make us different.”
The move to natural and antibiotic-free pork worked out well for Beeler’s. Now, the company is evolving again with the introduction of Beeler’s Heluka line. The Heluka branded pork will remain natural and antibiotic free, but it will also be marketed as non-GMO.
The transition begins
After the decision to go natural, Beeler’s pulled growth promotants and antibiotics from its feed rations and opened a retail store for its products in West Des Moines, Iowa. The store eventually took the form of a meat market and bakery, but Beeler wondered if the natural and antibiotic-free products provided significant value to the customers that shopped there.
“I think the thing that was more important was the fact that we were a family operation,” he says. “My brothers and I worked in the shop with our wives and our kids and people got to know us. I think that was more important, the fact that people knew where their meat was coming from and that it was a family operation.”
After eight years, Beeler decided the market had developed and grown enough to get into the wholesale side of the natural business. The family sold the retail shop and began looking for a plant. The Beeler family found a natural plant in the northwest corner of Iowa that was going out of business.
“We didn’t buy them or anything, we just kind of picked up the pieces and started evolving from there,” Beeler says.
The original Beeler’s farm in southern Iowa still produced pork in the conventional method as the company began its natural operations in northwest Iowa by working with other independent livestock producers to raise pigs to Beeler’s standards.
A look toward welfare friendly
Beeler’s early customer base included Wild Oats and some independent retailers like the Wedge cooperative in Minneapolis and Cid’s Food Market in Taos, New Mexico. Eventually, as the market evolved, Beeler’s became the exclusive pork supplier to Wild Oats along with supplying the co-ops and began to do some business with Whole Foods as well. Ultimately, Whole Foods acquired Wild Oats.
Beeler’s began doing significant business with Whole Foods and supplied large portions of the western half of the United States. When Whole Foods started to write its Global Animal Partnership (GAP) standards, animal welfare standards and humane raising standards, Tim Beeler sat on the committee and helped.
Helping Whole Foods write its standards for animal well-being resulted in Beeler taking a trip to Europe in the fall of 2004 to look at different farms there. By 2005 there were plans in the works for Beeler’s to start building a new facility.
“After seeing the welfare-friendly farms in Europe, we came home and tore down the factory farm and built our own welfare-friendly farrowing farm in northwest Iowa,” Beeler says. “On that particular farm, we don’t use gestation crates and we don’t use farrowing crates. The gestating sows are housed in large social groups, deep bedded and they can even go outdoors.” The farm was completed in the fall of 2005.
Up to the challenge
Once Beeler’s made the decision to do things differently, challenges on the production side presented themselves, but the company was dedicated to relearning how to raise pigs the way they were produced 50 years ago. However, there were some differences that Beeler’s needed to account for.
“We were trying to do this on a larger scale basis,” Beeler says. “So it’s not like we just had 30 to 50 sows to contend with, we had 2,000. So we were trying to see if we could build a larger welfare-friendly farm and make it work, and there were a lot of challenges.”
Once in production mode, those challenges began to pop up. The first thing Beeler learned pertained to the genetics of the sows. The previous operation relied on gestation crates and without them the sows had difficulty adapting to large social groups, Beeler says. “There was a lot of fighting and they got too big, so we had to select a different genetic strain.”
Beeler’s decided on Duroc boars from Europe crossed with European-based females to get the temperament they needed for the welfare friendly environment. Beeler says they found the sows to be more docile and friendlier in the open gestation system. “Their mothering characteristics were better in a box where they were not confined to crates,” he explains.
Along with a new strain of animal and the elimination of gestation crates, Beeler’s stopped using farrowing crates. At the start, Beeler’s saw a pre-weaning mortality rate of 50 to 55 percent. Beeler knew that a mortality rate that high would not only put the farm out of business, but was also inhumane. After six months of observation and study, Beeler’s came up with a redesign.
“The goal was, the sow is supposed to be able to stand up, turn around, be able to move, and lay down in full recumbency,” Beeler says. “So how were we going to accomplish that and yet save pigs?”
The newly designed box gave sows the ability to physically behave in accordance with the goals set forth. Protective bars were fitted to what Beeler refers to as a maternity box. The box gives the sow the room to exhibit the necessary behaviors, but the bars protect the pigs due to the sow’s ability to easily step over them.
“Those bars are placed in there in such a way that there is only one way for her to lie down and that is between the bars. And that gives the pigs a chance to get out of her way,” Beeler says.
The maternity/farrowing boxes were raised on wire, like the conventional style, allowing for nesting and keeping the sow and her pigs dry. Once the boxes were designed, remodeled and constructed to the spec necessary, the farrowing performance improved dramatically, Beeler says.
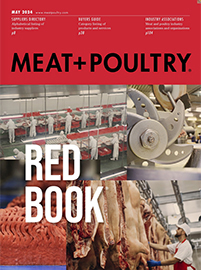