Manual operations
Unlike typical chicken operations, turkey plants require more manual processing. The variance of birds within flocks necessitates it. When a load of chickens comes into processing, weights vary in terms of ounces, but turkey weights vary by a pound or more, even if they’re from the same farm, Acosta says. Because of the size differences, automation can only be taken so far before yield and consistency begin to suffer.
“The machines are set up to go in at a certain point regardless of function,” Acosta says. “If a bird is different, it’s very challenging.
“Some folks are doing more automation than we are, but I would say the more automation you do, you’re making some sacrifice. Something has to give when you’re dealing with a turkey operation.”
The difference between processing hens and big toms simply means a different set up of the machines. The functions are the same. Skill sets among workers between the shifts vary only slightly and are outlined, along with safety and personal protective equipment (PPE) requirements, in what Cargill calls job task analysis. “If there is a slight change because of hens and toms it’ll be noted in that (job task analysis) for their training purposes, but for the most part they’re the same jobs, it’s just a bigger animal,” Acosta says.
The safety portion of the job task analysis is an important part considering the manual nature of processing at the Springdale facility. The plant participates in the Voluntary Protection Program (VPP), a partnership with the Occupational Safety and Health Administration (OSHA), and holds status as a star site. OSHA works together with a plant as an outside set of eyes to give perspective on processes and worker safety. There’s an open door policy with OSHA to discuss, audit and review onsite. “With the VPP program and opening the doors up to OSHA, it just creates an engaged workforce around safety,” Acosta says.
Springdale’s method of production relies on those working the lines and their performance. Acosta and his management team realize this and deeply appreciate the efforts of the workforce. “I consider myself truly blessed to lead such an amazing team,” he says.
Products at the Springdale facility include marinated tenders for retail, ground turkey in lean points of 85 percent, 93 percent, 97 percent, and 99 percent, fresh turkey patties, 1-lb. and 3-lb. chubs of ground for retail, 5-lb. and 10-lb. chubs for foodservice, both dinner and breakfast sausage, an assortment of modified atmosphere packaging (MAP) tray pack chops and tenders, as well as overwrap parts such as drumsticks, wings, thighs and necks.
Cargill, Springdale, produces products under the company’s Honeysuckle White brand in its Process Verified Program (PVP). The US Dept. of Agriculture (USDA) verified PVP ensures the brands’ turkeys are raised by independent farmers trained in animal handling without growth-promoting antibiotics, steroids and hormones. The PVP program applies to Cargill’s Shady Brook Farms products produced at Springdale’s sister facility in Dayton, Virginia, as well.
“We pretty much have redundant capabilities” Acosta says. “So occasionally if they’re running behind on something we can run some Shady Brook Farms product here and they run some product for us as well when we need some help.”
Automation where applicable
Acosta has worked at Cargill’s California, Missouri, operation, the Ozark facility and now at the Springdale location since 2004, making him a 23-year veteran with Cargill. His experience gives him insight into automation potential and the variables that make it successful without becoming detrimental.
Springdale’s packaged goods going into cases utilize automation to its fullest at the facility. After product moves down the Mondini MAP line, Bizerba vision equipment “sees” the top and bottom of the package simultaneously and ensures it’s the right product being cased. If a discrepancy is detected, it kicks the package offline for inspection and rework.
At the end of the Mondini line is the first robotic technology installed at the plant approximately 10 years ago. The Italian-made, CAMA packer places six packages at a time into boxes for shipping. The machine’s age makes it a little more complicated and it takes up more space than the newer CLP case packer it works alongside, “but it’s still a good machine,” Acosta says. “When you’re looking at automation, you have to look at your skilled maintenance to go with it,” he adds.
Acosta says advancing facility automation with machines to perform jobs once done by humans eventually creates a significant change in skill sets within the workforce. With more automation comes more operators and service technicians. Facilities need a different level of skill for success as automation increases.
“You can put all the automation in the world in, but if you don’t have the technical skills to maintain it then it’s a long hard battle.
“You look at all the packaging machines today, all the slicers, they all have computers and pro logic controllers; you’ve got to have the technicians to be able to troubleshoot and work on them and to keep them running,” he says.
Acosta emphasizes the people doing the work, whether manual processing, machine operation, maintenance or any of the tasks needed to keep the facility running, are still the most important variable. “Despite increased spending on automation, our people are our most valuable asset,” he says. “We could have all the greatest automation, processes and procedures in the world, but it’s our engaged team members that make us a success.”
Cargill works with a local technical school to help meet the challenge of hiring skilled labor. In addition, the plant offers tuition reimbursement and encourages employees that want to take classes to increase their skill sets and ensure their value with Cargill.
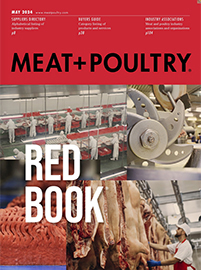