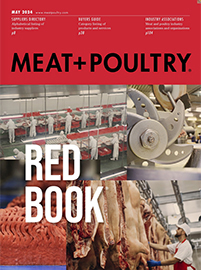
Enhance your industry IQ Sign up for our free newsletters to stay informed on each day’s news and trends |
Subscribe |
AUGMENTED REALITY FOR MAINTENANCE & TRAINING HOW CAN IT HELP?
In the past, engineers would have to wait for equipment to break down before conducting repairs. No set maintenance schedules existed, and diagnostics were inconclusive. Equipment was removed for service, accumulating hours or days of costly unplanned downtime, requiring on-site assistance from available third-party techs.
Today, augmented reality (AR) offers a better path towards efficient, proactive service and maintenance and collaborative remote training between meat packagers and expert OEMs.
Interconnected AR systems give service personnel the power to collect and monitor system health and performance data in real time, applying limitless diagnostic capabilities to their service, maintenance, and repair processes and offering interactive step-by-step instructions for flawless execution of service and maintenance processes.
WHAT IS AUGMENTED REALITY?
Yet harnessing the full power of AR means understanding its definitions. Augmented reality is a form of Smart Connected technology that creates an interactive digital twin of your existing packaging equipment, overlaid via video within your smart device (VR headset, glasses, tablet, or smartphone). This 3D mirror image acts directly in contact with the object, allowing for real-time service and training activities.
AUGMENTED REALITY FOR MAINTENANCE
Many meat packaging producers are adopting AR en masse for equipment maintenance, service, and repairs.
Operators use sophisticated AR tools, such as PTC’s Vuforia experience and ThingWorx software, to gather and track system data live and proactively create preemptive service alerts using condition-based monitoring and predictive analytics. Using this full suite of AR tools, they can identify root causes of component and system failures, receive actionable insights, and follow step-by-step interactive instructions to conduct service and repair activities to solve complex equipment issues.
Unlike traditional, reactive processes, these AR-based solutions prevent production interruption, unplanned downtime, and additional service costs from on-site technicians, saving meat packagers up to $250,000 per line in annual potential operating costs and optimizing performance and reporting.
HOW AUGMENTED REALITY BENEFITS MAINTENANCE
Augmented reality minimizes human error and maximizes system service efficiency. This optimization reduces repair means times, provides better availability for connected assets, and minimizes unplanned downtime.
But do AR’s benefits yield real, measured return on investment (ROI) to offset upfront technology and production costs?
Yes. We examine how:
Precision Data & Unplanned Production Downtime
AR provides a comprehensive understanding of your packaging system through precise performance, health, and compliance data over time. Technicians can use this data to eliminate guesswork, make actionable, data-driven decisions, solve complex challenges in hours, not days, and optimize human production efficiency to avoid unplanned downtime costs (up to $5670 per day on average).
Set Maintenance Schedules & Overall Equipment Effectiveness (OEE)
AR is the key to proactively creating set maintenance schedules for every connected packaging machine. These standardized schedules let operators monitor system health and compliance and dispatch the right internal or external technician with the precise service or maintenance solution to preemptively solve any issue. This condition-based monitoring and the resulting predictive analytics translate to higher OEE, one point of which has a production value of over $2 million annually.
AUGMENTED REALITY FOR TRAINING
AR is also instrumental in interactive application training. Responding to the labor demands of the new post-Great Resignation reality, packagers are turning to augmented reality to facilitate essential legacy knowledge transfer and advanced interactive instruction for technical staff.
Augmented reality tools allow technicians to interact with applications digitally during real-time training sessions using sophisticated 3D rendering technology on connected smart devices. Utilizing a digital overlay and recorded media, AR training takes service personnel through step-by-step diagnostic and repair cadences – alone or with an offsite specialist - to solve complex mechanical challenges. This process provides live feedback to ensure efficacy and the highest engagement, collaboration, execution, documentation, and learning.
HOW AUGMENTED REALITY BENEFITS TRAINING
The ROI in AR for training is efficiency optimization in task completion, data collection, and human productivity.
Data-Driven Efficiency
AR trains technicians to be faster, more accurate, and accountable when finishing service-based tasks. Using AR, packagers can achieve up to 20% increases in human productivity and collect invaluable productivity metrics that can reclaim up to 3000 hours of production time annually.
Legacy Knowledge Retention:
Packagers can experience up to 120% employee turnover in a calendar year, costing them up to $70,000 in onboarding and training costs per employee. AR training tools capture and store invaluable current service knowledge during training and live service functions, empowering technical teams to better retain legacy service knowledge, be more self-sufficient, and significantly lower training costs and Total Cost of Ownership (TCO).
THE FUTURE OF AR FOR MAINTENANCE & TRAINING
Meat packaging equipment is getting smarter. More systems are monitoring and maximizing OEE and minimizing downtime (up to 80%). Integrated AI systems are becoming the standard to facilitate self-adjustment and autonomously maintain peak performance.
Until then, forward-thinking meat packagers should empower their teams with accessible knowledge using AR for new and legacy systems to optimize equipment efficiency and human productivity.
Only through simplified service, operation, and data can we perfect how machines are used in meat production and how effectively they are serviced in the field.
Enhance your industry IQ Sign up for our free newsletters to stay informed on each day’s news and trends |
Subscribe |