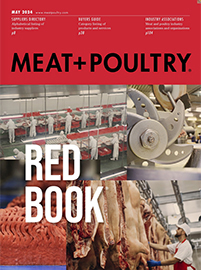
Enhance your industry IQ Sign up for our free newsletters to stay informed on each day’s news and trends |
Subscribe |
Maximizing yield at the processing plant is essential for maintaining profitability and ensuring long-term success for broiler producers as demand for poultry increases. Even the smallest improvement in uniformity can result in reduced processing costs and substantial financial gains for large-scale operations. Inconsistencies in bird size and weight complicates production, increases waste, and reduces efficiency. Therefore, ensuring birds are consistent weights and sizes is key to driving efficiency throughout the value chain, making it the most critical factor in yield maximization.
Hatcheries: The starting point for uniformity
Increasing yield starts well before the birds reach the processing plant—it begins at the hatchery. By accurately sexing broiler chicks early and implementing sex-specific rearing strategies, producers can improve live bird programs, reduce weight and size variability, and achieve greater flock performance throughout the grow-out phase.
Today, various sexing methods exist, both manual and automated, including vent sexing, feather sexing, and in-ovo sexing—each serving different industry needs. For large-scale broiler operations, feather sexing has emerged as the most suitable method for its high accuracy, cost-effectiveness, and less invasive process.
As the industry embraces automation, artificial intelligence (AI) is driving technological advancements across every production stage—from incubation to slaughtering. Companies like TARGAN are now offering AI-powered sexing systems, enabling broiler producers to automate their existing sexing operations with ease and opening the door for increased adoption of this lucrative practice.
How producers can optimize yield with uniformity
Yield is a critical metric for processing plants, directly impacting profitability by increasing the volume of salable products without raising operational costs, such as raw materials or labor. When flocks are uniform, plants operate more efficiently; equipment calibration is smoother, manual intervention is minimized, and carcass utilization improves. All of which are necessary for improving yield.
1. Improving primary processing
Overall, these improvements can reduce waste, prevent equipment inconsistencies, and minimize damage, which are important during meat recovery.
2. Improving secondary processing
These steps are where yield is maximized, as uniformity improves meat recovery and ensures efficient processing.
3. Improving further processing
By maintaining uniformity throughout these three stages, processing plants are able to maximize yield, minimize waste, and maintain high product standards.
Achieving the uniformity needed
If yield starts at the hatchery, then uniformity is integral from the start. Once sexed birds arrive on the farm, raising males and females in separate houses allows producers to fine-tune management for each group’s growth needs. Due to their different growth rates, this separation is key to optimizing development and use of resources.
By removing the competition for feed and water, growth is more predictable, resulting in better equipment utilization, enhanced access, and improved feed conversion ratios (FCR).
When birds reach the processing plant, their consistent size allows for smoother operations, precise equipment calibration, and higher yields. From hatchery sexing to farm management, these strategies deliver uniform birds, boosting efficiency and profitability across the production chain. Visualizing male and female uniformity In this example, broiler birds are raised to the same target weight of 2.7 kg (6 lbs) with a 10% weight range. The graphs visually compare the weight uniformity of straight-run (mixed-sex) flocks versus sexed flocks.
WingScan™: Enabling uniformity
Launched in 2023, TARGAN’s WingScan™ system revolutionizes sex identification at hatcheries using advanced vision systems and AI algorithms to sex and sort day-old chicks with up to 98% accuracy, processing up to 100,000 chicks per hour, depending on the system configuration.
By automating the sexing process, WingScan™ unlocks downstream value for poultry producers at the farm and plant. The system enables targeted feeding strategies to enhance bird uniformity, thereby optimizing production planning, increasing yield, and ensuring consistent product quality at processing plants. The downstream impact of implementing WingScan™ in hatcheries significantly boosts profitability throughout the value chain by reducing variation and maximizing efficiency.
For more information, go to www.TARGAN.com/WingScan.
Enhance your industry IQ Sign up for our free newsletters to stay informed on each day’s news and trends |
Subscribe |